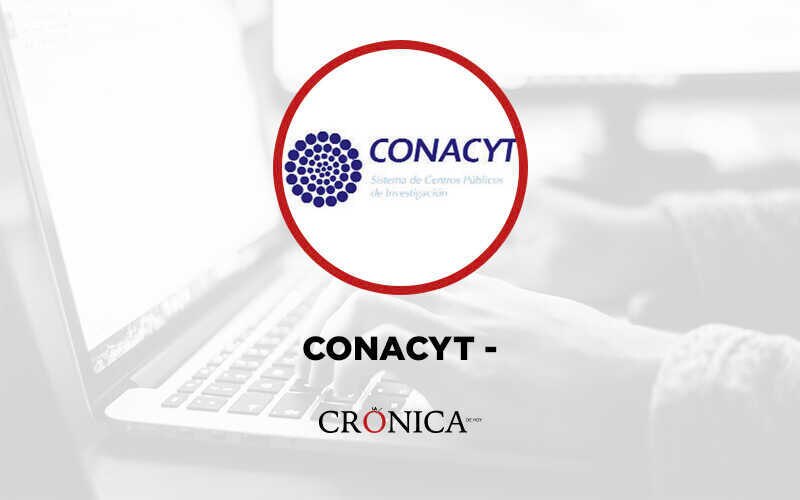
El desarrollo de materiales ecoamigables es cada vez de mayor interés para el sector automotriz ya que esto permitirá reducir la huella de carbono de los autos. De acuerdo a las proyecciones internacionales, se espera que la producción de materiales basados en materias primas renovables incremente hasta en 25 por ciento para el 2030, lo cual permitirá ir incorporando paulatinamente cada vez una mayor cantidad de materiales verdes en diversas aplicaciones.
Los materiales más ligeros que se utilizan actualmente en la industria automotriz son los polímeros y sus compuestos, especialmente aquellos reforzados con fibra natural, teniendo como principal enfoque la reducción del peso de los vehículos mediante el uso de estos materiales biocompuestos.
De manera general, a los compuestos formados por una base polimérica sintética con la adición de algún componente natural con la característica de provenir de una fuente renovable de origen biológico y biodegradable, se les denomina “Compuestos Verdes”, “Biocompuestos” o “Eco-compuestos”.
Aunque actualmente los materiales compuestos plásticos están adicionados o reforzados con partículas inorgánicas o fibras sintéticas (principalmente vidrio), estas últimas tienen la desventaja de ser más densas que la matriz. Además, utilizan una alta energía para su obtención.
Las fibras naturales tienen la ventaja de ser de menor costo, baja densidad, buenas propiedades mecánicas, son biodegradables y hay una amplia disponibilidad y variedad dependiendo de las regiones donde se produzcan.
De manera particular, en el caso de la industria automotriz, los compuestos verdes impactan de una manera muy significativa, principalmente en la producción de vehículos más ligeros. Esto no impacta únicamente en términos de costos sino también en una reducción de las emisiones de CO2 al ambiente. Se estima que la reducción de 25 por ciento en peso de los vehículos corresponde a una reducción de 250 millones de barriles de petróleo crudo y una reducción de emisión de CO2 de 220 millones de libras por año. Por esta razón algunas empresas automotrices como Volkswagen, Ford, Honda y General Motors utilizan fibras naturales en la producción de asientos, revestimientos y techos, paneles de puerta, sistemas para aire acondicionado, faseas y tableros, entre otros. Actualmente cada auto usa en promedio 2 kg de fibra natural y se espera incrementar la cantidad de fibra para la fabricación de autopartes debido a las ventajas que ésta ofrece.
Existen varios retos que deben superarse antes de incrementar el uso de las fibras para la fabricación de autopartes. Los principales son buscar nuevas soluciones que promuevan mejorar en mayor medida la adhesión interfacial con diversos plásticos para incrementar el desempeño mecánico de la pieza final; reducir la capacidad de absorción de humedad de la fibra, y mejorar la estabilidad térmica de la fibra para que se refuercen polímeros de ingeniería como es el caso de la familia de las poliamidas.
En este último aspecto, en el Centro de Investigación en Química Aplicada (CIQA) se ha desarrollado un procedimiento para mejorar la estabilidad térmica de la fibra de agave. Dicho procedimiento desarrollado por la Dra. Silvia Solís y el Dr. Ernesto Hernández consiste básicamente en impartir un tratamiento a la fibra en una solución básica con ayuda de ultrasonido. El ultrasonido es utilizado en la química debido al efecto de cavitación que éste provoca, el cual consiste en la transmisión de la energía ultrasónica a través de ondas creando compresión en la estructura molecular del medio en el cual se difunden. Dicho efecto incrementa la presión negativa del medio hasta lograr la formación de burbujas de cavitación que al chocar entre sí generan grandes cantidades de energía, acelerando así la difusión interna. Actualmente esta tecnología es utilizada en la industria química y textil, principalmente para facilitar la eliminación de sustancias consideradas como de suciedad, erosión, descomposición de partículas y para la realización de desengomados. También se utiliza para la síntesis de polímeros, dispersión, funcionalización de nanopartículas en diversos medios y como tratamiento superficial para fibras naturales.
En lo referente a la estabilidad térmica, se encontró que la fibra tratada tiene una temperatura de degradación de 250 ºC mientras que la fibra no tratada su temperatura de degradación comienza a partir de los 170 ºC. Este incremento en la estabilidad térmica asociado a la remoción de los componentes mencionados previamente, abre la oportunidad de elaborar compuestos reforzados con estas fibras tratadas con polímeros de ingeniería como Nylon 6, polietileno tereftalato y a otros, sin que las fibras sufran degradación o generen una apariencia no deseable en las piezas a desarrollar.
Este trabajo ha sido soportado por el Laboratorio Nacional en Innovación y Desarrollo de Materiales Ligeros para la Industria Automotriz (LANIAUTO) que es parte de la Red Nacional de Laboratorios del Conacyt. Como parte de una de las líneas estratégicas de investigación de este laboratorio que es el “desarrollo de materiales sustentables para la industria automotriz”, actualmente se están realizando las pruebas para probar que dichas fibras tratadas son capaces de soportar mayores temperaturas para preparar biocompuestos de ingenería para este sector.
*
Investigador catedrático del Centro de Investigación en Química Aplicada
Copyright © 2018 La Crónica de Hoy .